Explanation of Motor Cooling Technology
|
|
5. Explanation of Motor Cooling Technology
1. Introduction
The history of electric vehicles (EVs) began when Robert Davidson built the world's first EV. In Japan, the first domestic electric vehicle prototype was built in 1911, and an EV using an alternating-current motor was developed in 1983. Then, in 1997, the Toyota Prius, a hybrid electric vehicle (HEV), was introduced to the market, marking the dawn of the HEV era. (In 2004, approximately 130,000 HEVs were sold.)
With the progress of practical applications for HEVs, demand grew for a compact, high-performance electric motor for installation in the limited space of a vehicle. However, this requires an increase in output torque per motor volume, which in turn requires the improvement of thermal performance to achieve efficient cooling the large quantity of heat generated from limited heat radiating areas of such motors.
This document describes the following basic principals necessary for the thermal design of EV/HEV motors, and also discusses the prospect of future development trends.
* Principle of heat generation by motor operation (copper energy loss, iron energy loss)
* Various types of motor cooling systems (water-cooling, oil-cooling, air-cooling)
2. Items related to the thermal performance of motors
As described in the diagram below, thermal performance depends on three factors: heat generation, heat transfer (cooling), and permissible temperature.
When an electric motor operates, it generates heat. Heat transfer is necessary for discharging this heat from the motor. The temperature of each part of the motor increases based on the balance between heat generation and heat transfer. The sections that are susceptible to heat damage such as coils and magnets, must have sufficient heat resistance to withstand high temperatures.
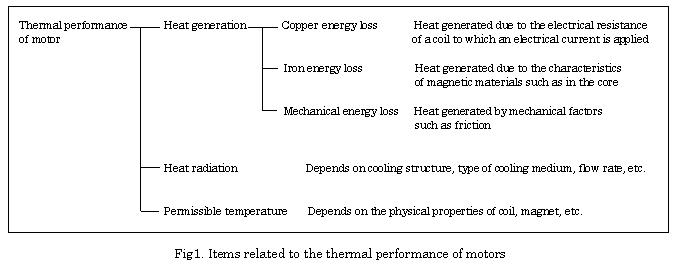
3. Heat generation of motors
Since all present motors consist of electrically conductive materials and magnetic materials, generation of heat cannot be avoided. In the following, heat generated by copper energy loss, iron energy loss, and mechanical energy loss will be explained in that order.
3-1. Copper energy loss
When an electrical current flows through a coil, the electrical resistance of the coil causes a copper energy loss, resulting in the generation of heat. For a three-phase alternating-current motor, the copper energy loss can be expressed by the following equation.
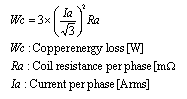
As the above equation indicates, copper energy loss is increased in direct proportion to the square of the electrical current. This indicates that, in an operating motor, copper energy loss is a dominant factor (when a large-current is applied -- that is, in the low-speed high-torque range of operation (see Fig. 2).
3-2. Iron energy loss
Iron energy loss can be divided between hysteresis energy loss and eddy-current energy loss. Generation of hysteresis energy loss is attributable to the physical properties of the magnetic steel plate (core) that forms magnetic circuit in the motor. Specifically, hysteresis energy loss is caused by the change in the magnetic flux density which results from the change in the magnetic field due to rotation.
Magnetic materials exhibit the characteristics shown in Fig. 3 when the magnetic field varies, which are known as hysteresis curves. The area enclosed by the hysteresis curves represents the loss. The hysteresis energy loss is determined by the following formula.
Next, eddy-current loss will be explained. When the magnetic flux in the core fluctuates, and eddy current flows around the magnetic flux lines. The eddy-current energy loss resulting from the electrical resistance to this current generates heat. Heat is generated not only by the core but also by the magnets. Since this heat generation can reduce the magnetic force of the magnets, special attention must be paid to eddy-current loss.
The iron energy loss -- both hysteresis energy loss and eddy-current-loss -- increases with operating frequency. Therefore, a motor generates more heat when it operates at a higher rotating speed range. (See Fig. 2.)
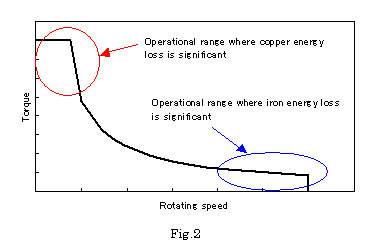
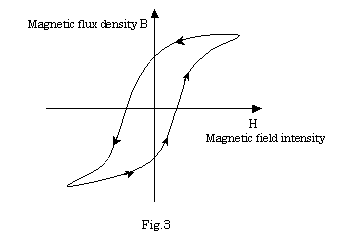
3-3. Mechanical energy loss
Mechanical energy loss occurs mainly due to the friction in bearings and the resistance of air caused by agitation of the air at the gaps between the rotor and stator. Although mechanical energy loss is normally less than the copper energy loss or iron energy loss, it must be taken into consideration when a strict examination of heat generation is conducted.
4. Cooling of motors (heat transfer)
The heat generated by the operation of a motor is temporarily stored in the heat capacities of the materials making up of the motor. For continuous motor operation, however, the motor must be structured to allow the transfer of heat from the motor. Generally, a motor incorporates an air-cooling, water-cooling, or oil-cooling system for that purpose. The basic difference among these three systems is the type of cooling medium used.
4-1. Air-cooling system
The air-cooling system removes heat from a motor by directing the air flow created or by using a cooling fan for this purpose.Some motors feature fins on their surfaces to facilitate heat radiation from the motor units, while some motors are designed to draw outside air directly into the motor for cooling. The air-cooling system does not require any cooling medium circulating equipment or cooling device; thus, the structure can be simple.
However, the air-cooling system cannot provide high cooling performance due to the limitations of air's heat transfer coefficient. Another drawback is that the cooling capacity varies depending on the ambient temperature. Many train motors currently use an air-cooling system, but as trains motors have been required to provide high output in a range of 170 to 190 kW (per-hour rating) in recent years, the cooling system used in such motors is shifting from air-cooling to water-cooling to cope with the increased heat generation. For HEVs, the IMA System equipped in the Honda Insight and Civic employs an air-cooling system.
4-2. Water-cooling system
A water cooling system removes heat from a motor by sending water through water channels included inside the motor unit and then cooling the water before circulating through the motor.By using a radiator, a water-cooling system can maintain a constant water temperature and provides high and stable cooling performance. Additionally, the cooling capacity can also be adjusted easily by varying the flow rate of the circulating pump.
To create water channels, a concentric double casing structure is often used for motor units made of aluminum casting so that a water channel is formed around the entire outer surface of the motor unit. In some cases, water passages are provided on certain sections of the outer body.
The water-cooling system has some shortcomings. The unit structure becomes complex due to the water channels, and there is the need to provide space for the installation of cooling water pipes, a radiator, and other components inside the motor compartment. In addition, the circulating pump consumes electricity.
Use of a water-cooling systems is becoming increasingly common for high-performance motors. For example, the Toyota Prius utilizes a water-cooling system.
4-3. Oil-cooling system
The oil-cooling system is basically the same as the water-cooling system in principle, but it uses oil, instead of water, as the cooling medium. This system also boasts high heat transfer.Unlike water, oil has an insulating characteristics. By circulating oil inside a motor, the heat generating sections (coils, core, magnets, etc.) of a motor can be cooled directly and efficiently.
However, just as in the water-cooling system, the oil-cooling system requires pipes, oil cooler, circulating pump, etc., and the structure of the cooling system becomes complex. It is also important to note that, if the structure allows oil to enter between the rotors and states, friction resistance (mechanical energy loss) can be generated by the oil.
4-4. Determination of the thermal performance of a motor
In a simple model, the following equation can be used to determine the relationship between the heat generated by the motor and the amount of heat released.
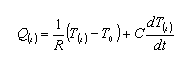
The left side of the equation is the quantity of heat generated by the motor. The right side of the equation expresses the amount of heat transferred from the system by cooling and the amount of heat absorbed by the heat storage capacity of the motor.The temperature of the heat generating section, the temperature of the cooling medium, the heat resistance value, and the thermal capacity are indicated by T(t), T0, R, and C, respectively.
Here, the amount of heat radiation is

The lower the heat resistance value and the greater the temperature difference between the motor and cooling medium, and the greater the quantity of transferred heat becomes. The heat resistance can be reduced by optimizing the structure between the heat generating sections and the cooling medium passage in order to improve heat conduction efficiency as much as possible. The heat resistance value can also be made smaller by increasing the flow rate of the cooling medium.
In the actual design of a motor, the setting the heat resistance value related to the heat transfer performance is most critical.For a motor for which high continuous operation performance is required, in particular, the performance depends almost entirely on the motorfs heat resistance.If the motor does not require high continuous performance but operates frequently under overload condition, the heat storage capacity of the motor materials for temporary storage of heat must be given consideration in the motor design.
Generally, high continuous operation is required for an EV motor because that motor is the sole source of driving force for the vehicle.In an HEV (parallel hybrid system, etc.), on the other hand, a motor and an engine are combined for providing drive power. In this type of vehicle, the motor is often used as an assist power source and operates intermittently; therefore, performance in overload operation is more important than continuous performance in the motor for an HEV. Consequently, the thermal performance of the motor must be determined by taking into consideration how the drive system uses the motor.
5. Future development trend
Improvement in heat performance has been made in terms of heat generation, heat transfer and permissible temperature , which are the key factors in the heat performance of a motor.
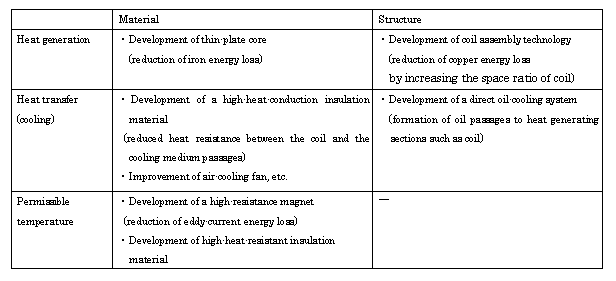
|
|