On the initial publication of technical explanations
I would like to start publishing comments regarding the technologies of electric drive especially for those that are currently restricting efficiency or output during the process from energy generation to driving torque.
1. Power semiconductor device(When is the limit of silicon overcome?)
In 1983 an EV powered by an AC motor was introduced into the market for the first time in Japan. This was made possible by the practical use of IGBT for power control which was brought about by the technological advancement of semiconductors. With the use of an AC motor, the overall efficiency of the vehicle driving control in which the efficiency at a high torque is important has improved significantly.
Switching loss of IGBT is greater than that of MOSFET but it can withstand a higher voltage than that of MOSFET making, which makes its widespread use of vehicle drive at a power supply voltage between 300V and 400V possible.
However, as the control speed is increased, switching loss also is also increased. In addition, since voltage loss occurs constantly at pn joint, efficiency is low at operating conditions less than the rated load. Accordingly, a MOSFET which can withstand high voltage has been long awaited.
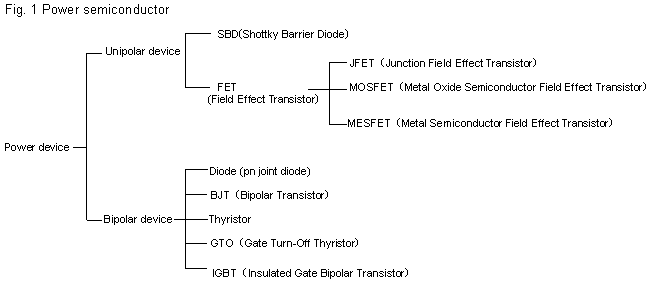
In Japan, a NEDO project, gDevelopment of Ultra Low Loss Power Devices Technologyh, was completed in March 2004, and the era of commercial use of SiC power devices has begun.
One advantage of SiC crystal (4H-SiC) is the high voltage it can withstand (breakdown field strength Ec). Therefore, the characteristic thickness of the semiconductor layer can be reduced. Since on-resistance can be theoretically designed inversely proportional to the third power of Ec, it is possible to substantially decrease the loss caused by the current. In addition by increasing the power supply voltage, the current is decreased and the system, including the motor, can be downsized.
Since it has a high thermal conductivity and it can be operated at a high temperature, it is possible to design an air-cooled device package to downsize the system significantly.
Next, I would like to explain issues regarding commercial use of SiC power devices.
Why is it that commercial use of the SiC device has not yet been achieved despite the fact that there are several advantages as mentioned above?
In the past it was difficult to manufacture a monocrystalline wafer and its yield was low making it commercially unviable. Currently a 4 inch wafer is available.
Another problem that makes it difficult to commercialize the device is manufacturing technology.
In 2002, a German company, Infineon, introduced a shottky diode of 600V-6A into the market. It can be said that the application of diodes began in order to downsize and reduce loss of power supply.
Currently, because there are failures caused by crystalline defects of the SiC bipolar device, commercialization of the device deems to be difficult.
There are two switching devices made of silicon semiconductor, IGBT and power MOSFET. With SiC, MOSFET whose on-resistance is 10m¶/cm2 or less has not been realized. Since carbon exists on MOS, interface channel resistance is thought to increase.
In June 2004, the National Institute of Advanced Industrial Science and Technology (AIST) reported a device which shows a type whose channel mobility is 230cm2/Vs. The practical use of this type of manufacturing is being awaited.
The advantages of these devices when applied to electric drive are summarized as follows.
1. Improvement of the efficiency of DC-DC conversion
Voltage control is necessary when discharging to a load. By using these devices, the optimum voltage and current for each load can be chosen. There is a considerable advantage for the system, such as reduced harness diameter, downsized relay to deal with high voltage as well as a simplified cooling system due to the adoption of a higher voltage motor and reduced voltage loss.
Additionally, due to increased efficiency of electric power transmission and charging, the total generation of CO2 of the electric energy path is substantially decreased.
2. Improvement in inverter efficiency
The inverter efficiency of Si IGBT is currently approx. 90% when under vehicle driving conditions. If the efficiency is increased up to approximately 98% of its physical property limit by adopting SiC, the driving range will improve by 10%.
However, the normal use driving range will improve by nearly 30% due to a ripple effect of changes to the characteristics of the vehicle, which will lead to significant reductions in aerodynamic resistance, weight, and power consumption of auxiliary devices due to downsizing the radiator.
References:
gFoundations and Applications of SiC devicesh
Jointly edited by Kazuo Arai and Sadahumi Yosida
Magazine Bureau, Ohmsha Ltd
(URL http://www.ohmsha.co.jp)
|