Regenerative braking
The disadvantage of electric vehicles is their lower range per charge in comparison with gasoline-fueled vehicles. Regenerative braking is a way to extend range of
the electric vehicles. In many hybrid vehicles cases, this system is also applied hybrid vehicles to improve fuel economy.
Regenerative braking refers to a system in which the kinetic energy of the vehicle is stored temporarily, as a accumulative energy, during deceleration, and is reused
as kinetic energy during acceleration or running.
This type of energy, for example, the kinetic energy of the flywheel and the accumulated energy of the accumulator are shown in the Fig. 5.142. However, it is generally
applied to systems in which the motor for running is activated as a generator during deceleration and the electric energy generated by the generator is stored in the main
battery or the capacitor.
The regenerative braking force is controlled by the accelerator pedal and the brake pedal, or switches. The regenerative braking control is used as follows.
Generally, the accelerator pedal controls the traction torque. Reducing will activate the regenerative braking, or keeping off from depressing the accelerator pedal.
Namely, deceleration similar to the engine braking of the gasoline-fueled vehicle is generated. In this method, a simple mechanism can be provided because neither a sensor for
activating regenerative braking nor an actuator for adjusting the hydraulic pressure braking force has to be provided.
From the reason of drivability, a large braking force cannot be given. Therefore, a lot of energy recovery is not expected.
When the regenerative braking is used for foot braking, a deceleration force of 1G MAX is required for the gasoline-fueled vehicles. When regenerative braking is used in electric vehicles,
however, such a large braking force cannot be generated because there is a limit of capacity for the motor, inverter and main battery. To solve this problem, a hydraulic brake is also used.
For example, a diagram of the brake system used for the TOYOTA RAV4LV EV is shown in Fig. 5.143. When a driver applies the brake, hydraulic pressure is generated and detected, and the EV ECU
controls the inverter so that the motor generates negative torque corresponding to the hydraulic pressure. The electricity generated here is stored in the battery. Within the limit of the braking
force generated by the motor, the regenerative braking force is generated, and then the hydraulic braking force is controlled by cooperative control valve of the regenerative braking. In this way,
the energy loss caused by the frictional heat is suppressed as much as possible, and amount of the energy recovery is improved. If a braking force beyond the capacity of the regenerative braking force
is required, the hydraulic braking force is generated to make up for the deficiency. Unlike gasoline-fueled vehicles, electric vehicles do not have a negative pressure generation source that boosts up hydraulic pressure.
Thus, a power source is required. In the case of the RV4LV EV, a hydraulic booster is used with the electric hydraulic pump.
The flow of energy while braking is shown in Fig. 5.144. In order to store as much energy as possible, it is best to decrease the amount of every kind of energy lost.
In the cooperative regenerative braking system (figure. 5.145) installed on the TOYOTA PRIUS, the linear control valve is used in the hydraulic circuit, and the efficiency of the regenerative braking is increased by controlling
the hydraulic brake continuously in response to the regenerative torque which changes according to the vehicle speed or the recharging of the battery.
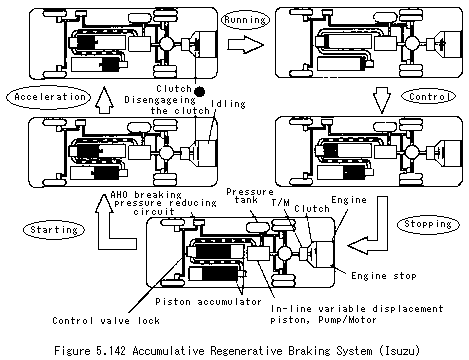
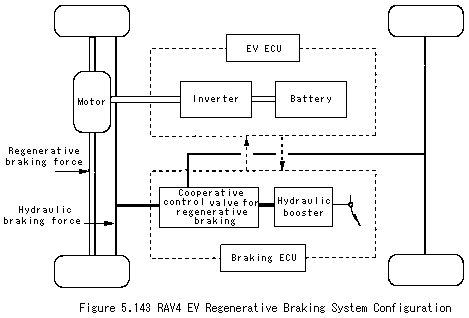
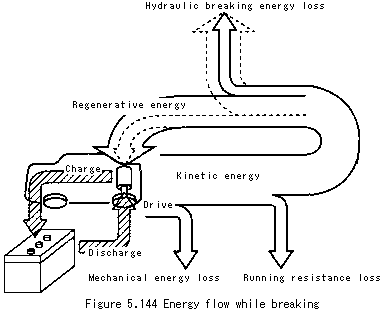
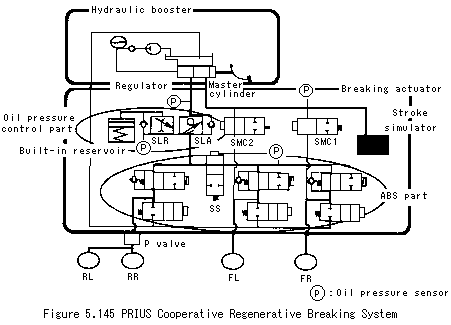
Reference
Book title: EV Handbook
Written by: EV Handbook Publisher's Group
Published by: Maruzen Co., Ltd. (URL http://www.maruzen.co.jp)
|
|